モーターコイル修理
新幹線や在来線の電車のモーターコイル、エレベーター、直流モーターコイルなどさまざまなモーターコイルの修理を行っております。
小型のモーターよりもかなり大型のモーターコイルの修理を得意としております。
もし、お使いの製品のモーターコイルの修理が必要な場合または、オーバーホールが必要な場合には一度ご相談下さい。
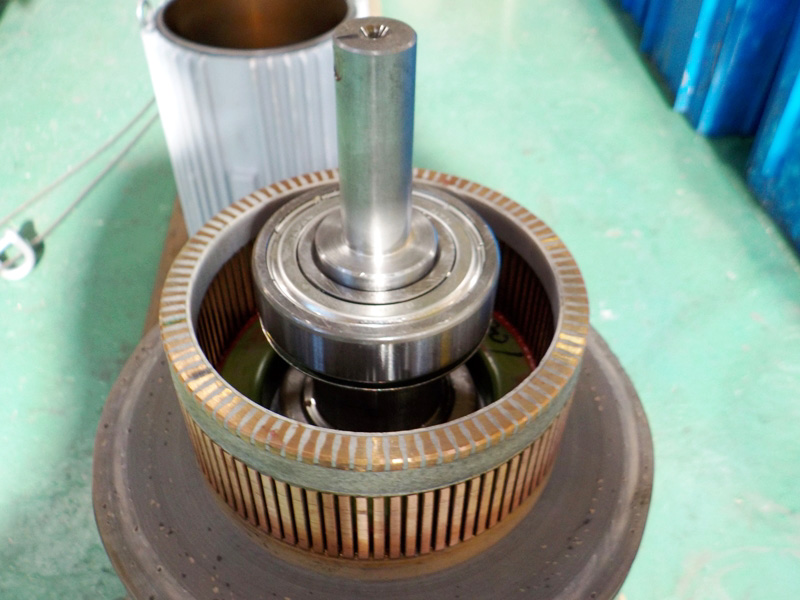
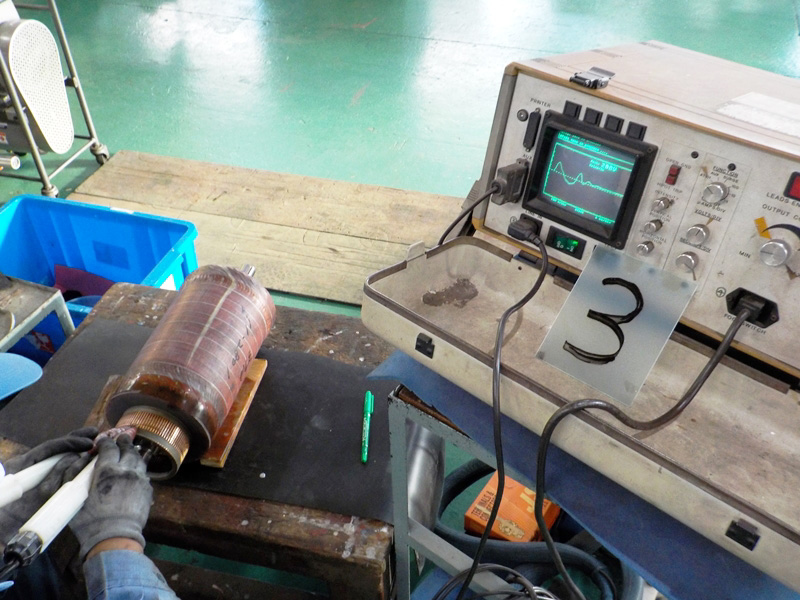
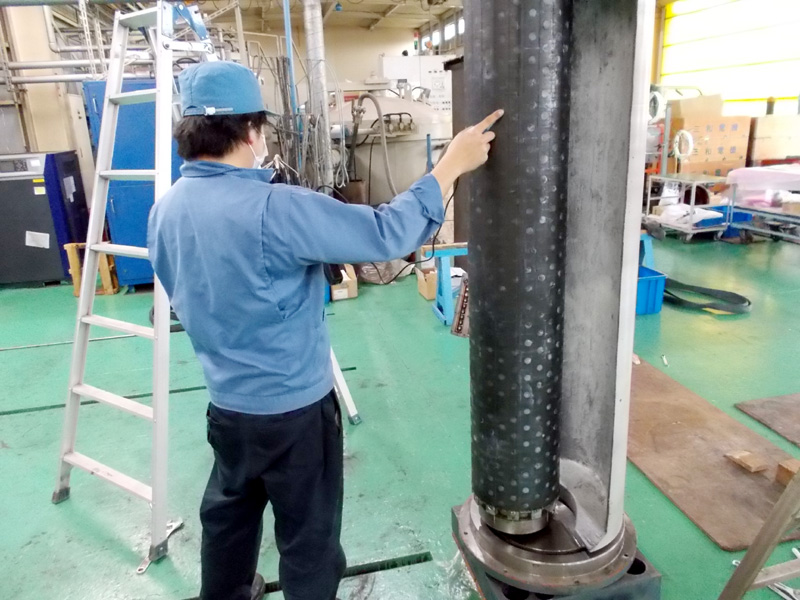
モーターコイル修理のよくある質問
モーターの容量はどのくらいまで対応可能でしょうか?
モーターの電圧はどのくらいまで対応可能でしょうか?
直流モーターの修理は可能でしょうか?
制御系が更新でない事情等で、直流モーターの修理依頼が増えています
特殊モーターの修理は可能ですか?
1年の期間をかけて修理した特殊直流モーターもあります
海外製のモーターも対応できますか?
ドイツ製のモーター等引合いがございます
中国・韓国製のモーターは対応可能ですが、新品価格近くになるケースが多いです
出張修理は行っていますか?
定期的なメンテナンスは可能でしょうか?
カーボンブラシの取扱いは、ありますか?
修理期間と金額は、わかりますか?
モーターの外観・銘板写真をメール送付いただき、故障状況が分かりますと、概算でのお答えは可能になるケースが多いです
モーターコイル修理の流れ
1、現品受け入れ
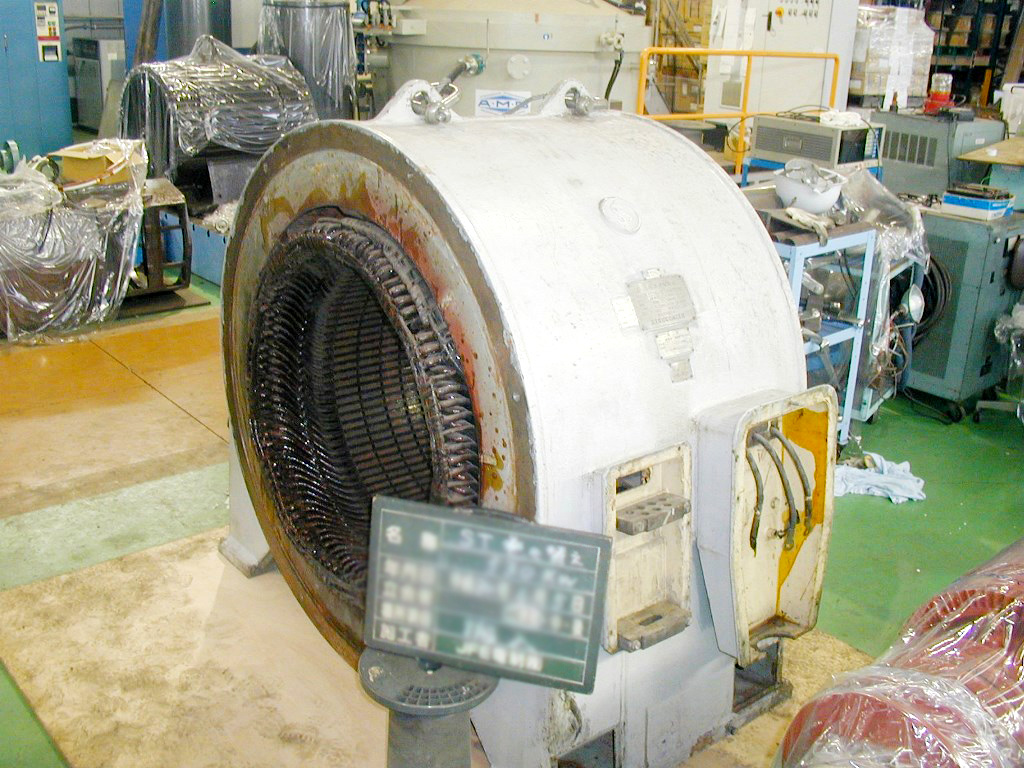
2、原姿記録
写真撮影
電気試験
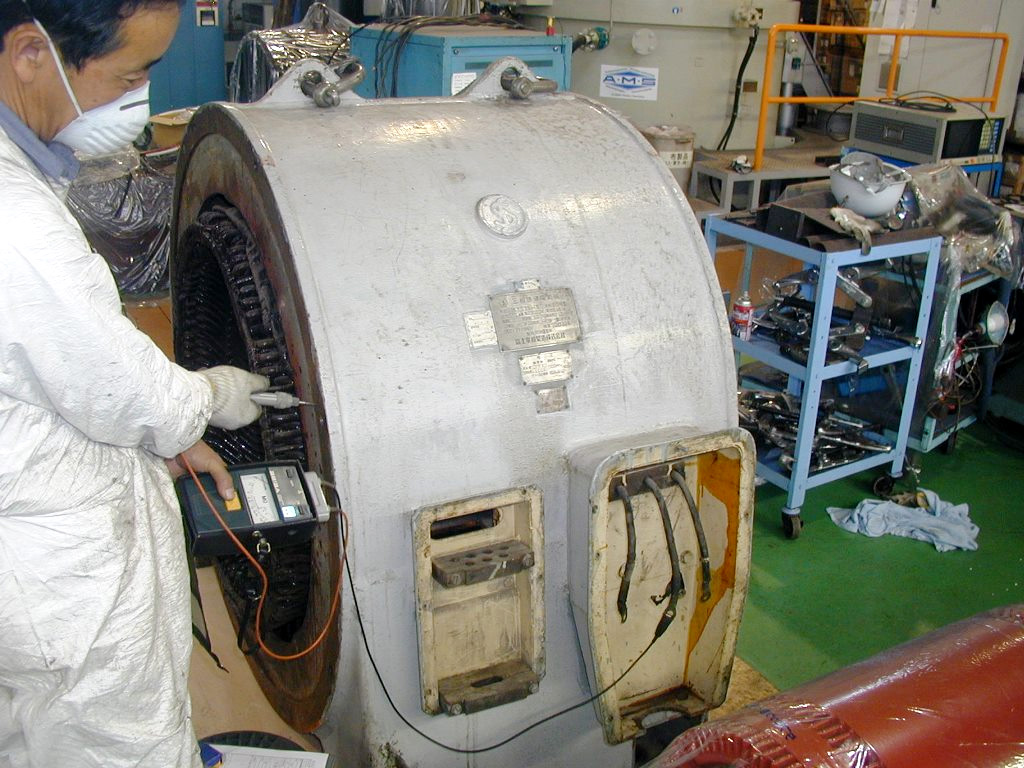
寸法記録
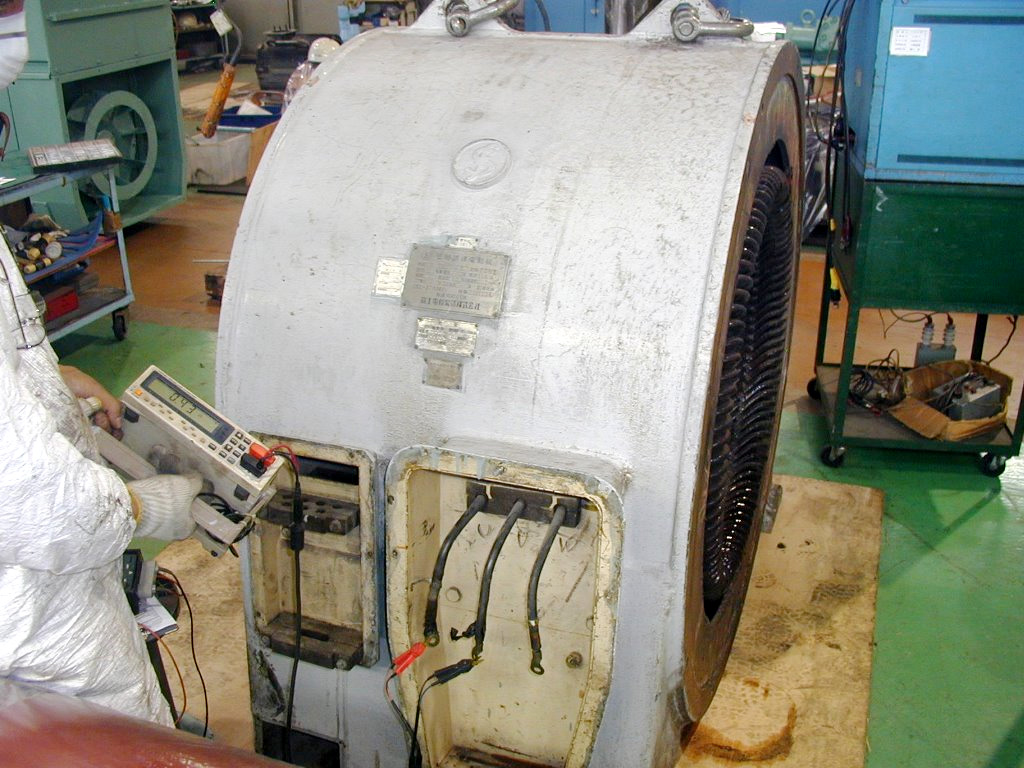
U・V・W・X・Y・Zの表示
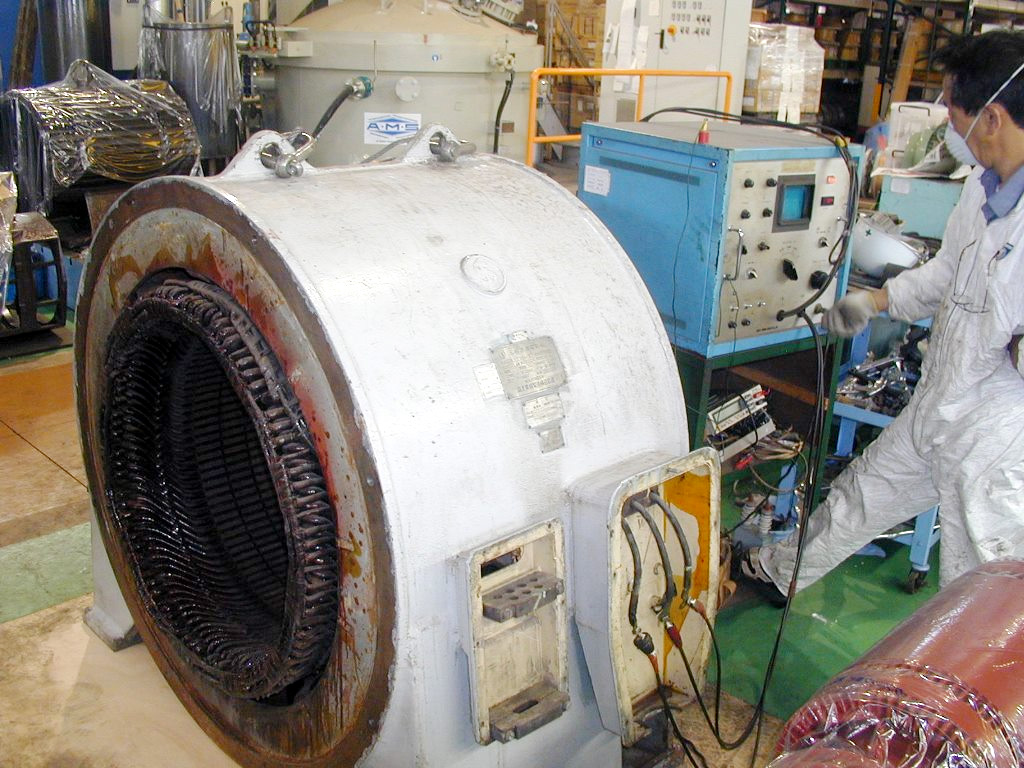
むし焼き出来ない物の判定
必コイル重量計算用データ採寸
コイルエンド切断
3、分解
蒸し焼き
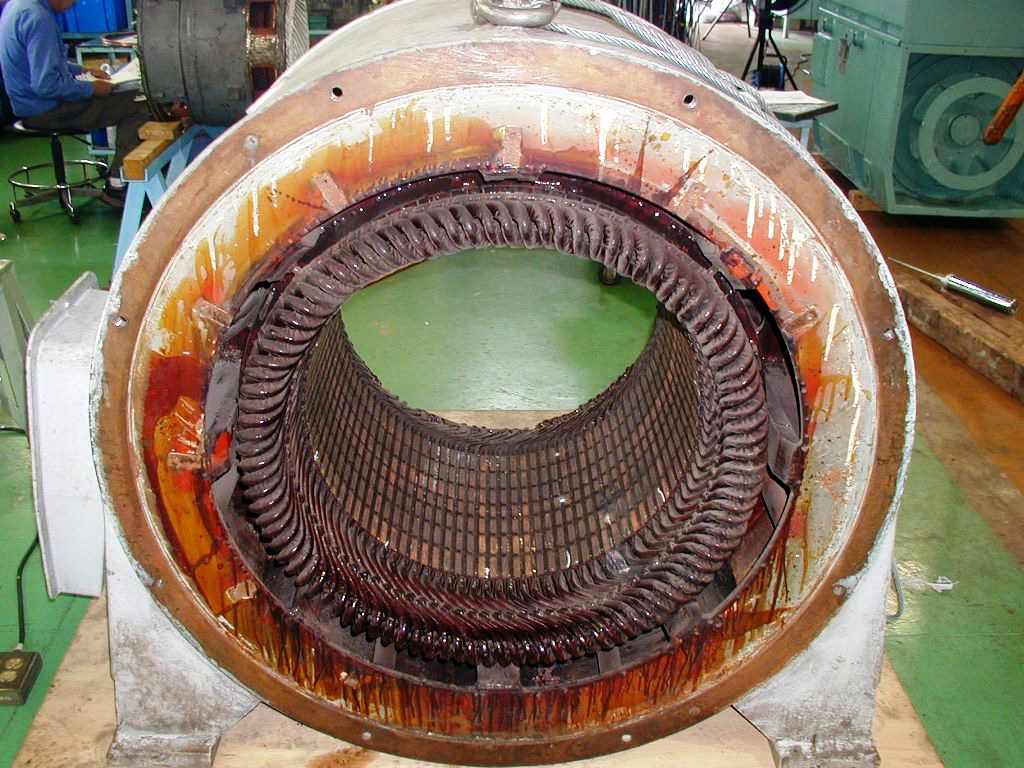
配線記録
接続図にU・V・W・X・Y・Zを記入、下口渡りを記入、上口渡りを記入、接続図(SM4-0210-1108~1120)、結線法、スター・デルターSTクミ仕様(SM4-0210-1089)
写真撮影
口出し長さ採寸
絶縁の長さ採寸
コイル揚げ
(3)揚げコイル分コイルエンドを切り、上コイルを揚げる。(4)コイルピッチを確認する。(5)1極1相コイルを揚げ保存。(量産化のタイミングで廃棄)、(6)反結線側のエンド部を切り(丸線)上口コイル下口コイルの順に揚げる。
ピッチの確認
4、清掃
エアーブロー
コアスロット溝清掃
フレーム清掃
クサビ溝清掃
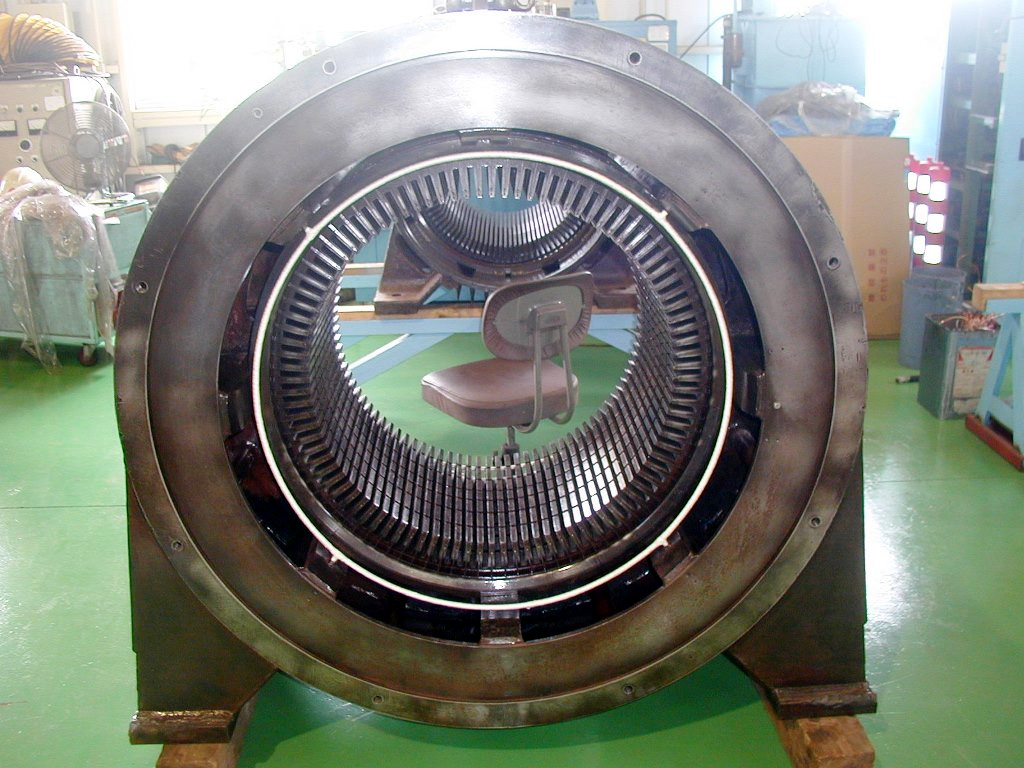
コア養生
エアーブロー
コア溝寸法測定
結線方向明示
コアニス塗りフレーム錆止め
写真撮影
5、コイル巻き作業
試しコイル作成
コイル寸法取り
巻型取付け
電線ドラム取付け
コイル巻き
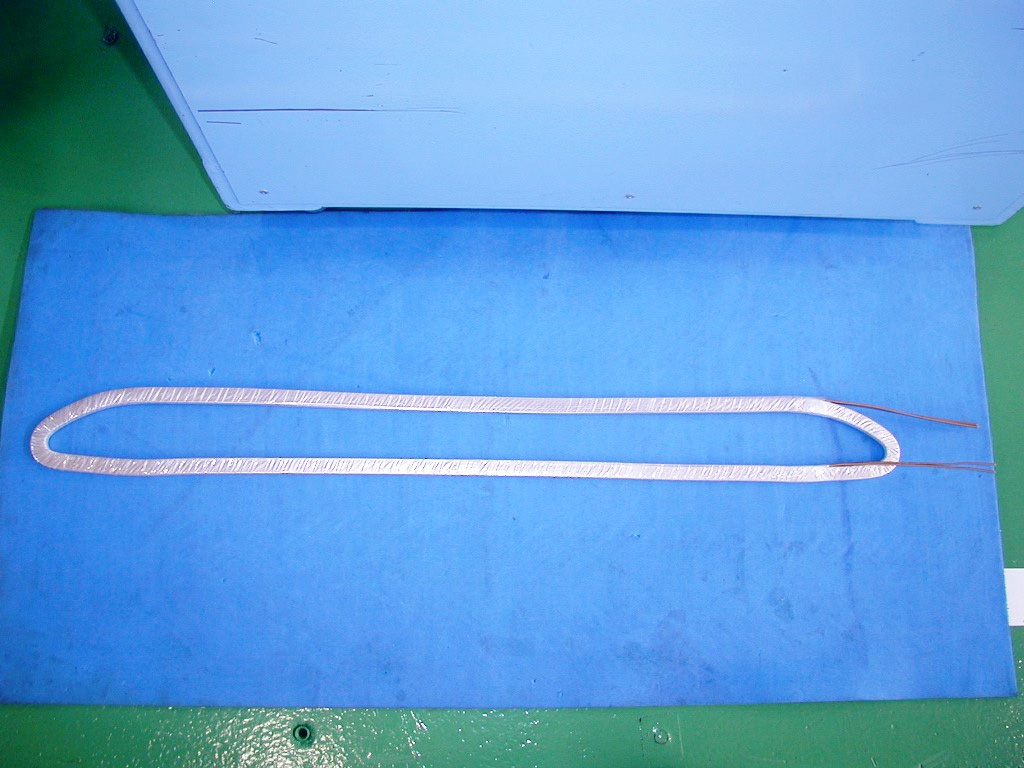
コイル取り外し
引き成形
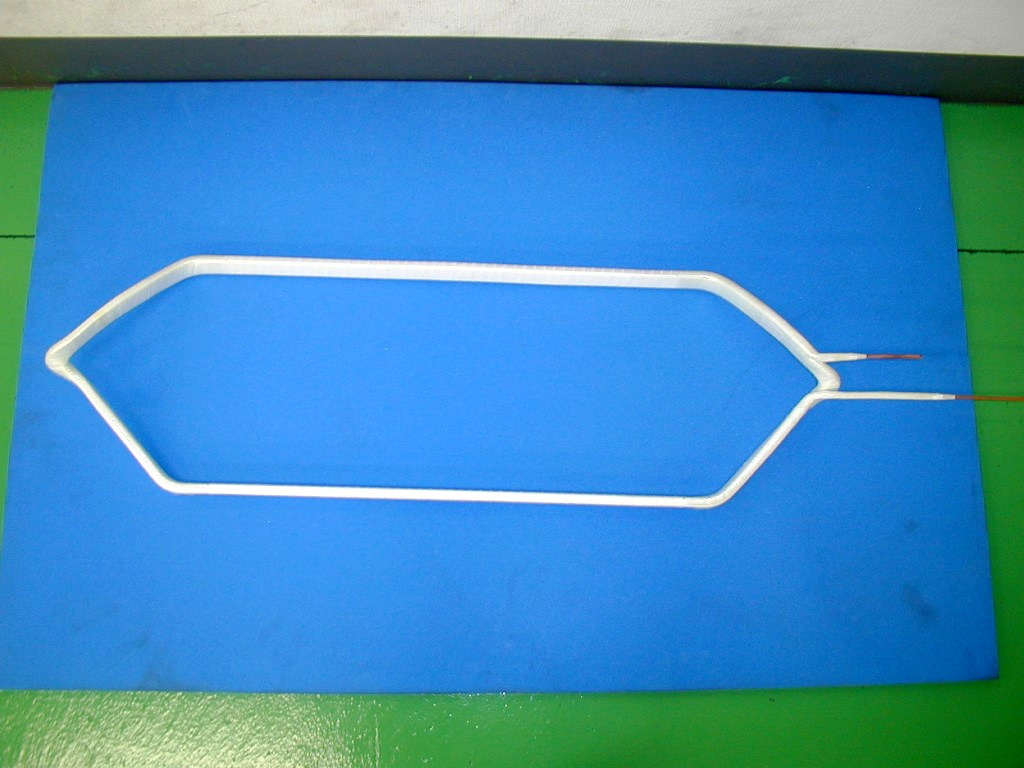
コイル寸法を測定チェックする。*モデルコア又はST鉄心に入れコイルエンドの隙間、角度を確認する。
引き成形の結果、寸法等問題がある場合は巻型修正を行う。修正巻型による試し巻コイルの引き成形を行う。
コイル寸法を測定、モデルコア又はST鉄心に入れコイルエンドの隙間、角度を確認する。引き形機データをST試作コイルDRレポート(SM4-0210-1005)に記録する。
巻型寸法をコイル巻~成形チェックシート(SA-013-3001)に記録する。
コイル巻き 巻型取付け
電線ドラム取付け
コイル巻き
口出し長さ分を考慮しておくこと。ブレーキを調整する。
電線を、ヘラで叩き、十分巻型になじませながら図面指定回数巻く。 *電線のつなぎは行わないこと。コイル巻き時のキズ、被覆の破れ、ラップ等をチェックする。巻き終えたら、紐で結わく。口出し寸法を確認して切断する。
コイル取り外し
口出し皮むき(DGC線、エナメル線及びハンダメッキ指示ある場合)巻始め、巻終りの電線被覆をむく。
口出しメッキ(ハンダメッキ指示ある場合)
検査(中間確認)
写真撮影
6、コイル引き・成形作業
締め付けテープ巻き
保護紙の寸法は、コイル巾+約10㎜とし長さは約50㎜とする。傷防止用保護紙はA~Hに入れる。
保護紙は面をコイルに当てること。
保護紙はコイル巾に対し片側約5㎜づつ折り重なるようにすること。保護紙のA、B、D、Gは、図1のように表面側に当てる。
保護紙のC、E、F、Hは、図2のように表面側に当てる。巻き終りのテープの止めは糊を良くつけ確実に止めかつ、糊をつけない部分を約10㎜残しテープを切る。
引き成形
引き成形の結果、寸法等問題がある場合は、引型機の調整を行う。OK時残りのコイルの引き成形を行なう。
コイル寸法を測定、モデルコア又はST鉄心に入れコイルエンドの隙間、角度を確認する。(コイル巻~成形チェックシートSA-013-3001に記録する。)
口出し成形
成形寸法測定結果をコイル巻~成形チェックシート(SA-013-3001)に記録する。
皮むき半田(皮むきがされていない場合)
検査(中間確認)
写真撮影
7、コイル絶縁
口出し絶縁
スロット絶縁
エンド絶縁
コロナ防止テープ巻き(一挙含浸方式時)
エンド部 仕上げテープ巻き
指定チェックシートに記録する。記録本数は、1台当たりの本数の10%を目安とする。”
検査(中間確認)
指定チェックシートに記録する。耐電圧試験を行う。(図面指示又は8kV、1分間印加のこと) :一挙含浸方式時*パトライトを使用し、周囲の人の注意を促がすこと。指定チェックシートに記録する。”
写真撮影
8、コイル入れ
コアの結線側と基準スロット
STコア清掃
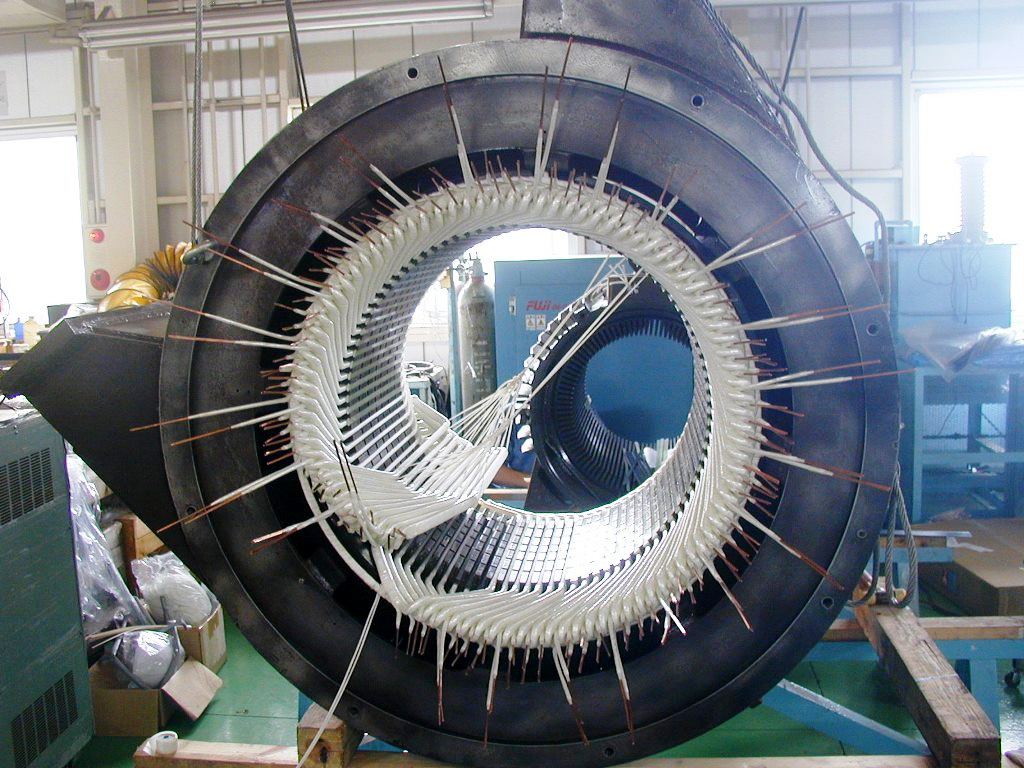
*特にスッロト部にはコアの出張り、スパッタの付着等有害物が残っていないことを確認すること。(コア・スロット等に溶接スパッタやバリが残っていないか、目視点検する。残っている場合は、前工程へ手直し依頼する。)
リングの取り付け状況
コイルサポート取付け
コイルサポートを指定位置に取り付け仮止めする。
コイルサポート作製
測温素子取付け
ゼツエンイタに測温素子を載せ絶縁し、低抵抗コロナ防止塗料を塗布する。測温素子の口出し長さを決め切断、被覆をむく。
配線用口出し線の測温素子側の被覆をむく。測温素子口出し線を先端から約30㎜のところで
切断して、再度被覆をむく。
配線用口出し線と測温素子口出し線を圧着端子アタP-2で圧着接合する。接合部1本ずつSR収縮チューブをかぶせ、収縮させる。
シリコンワニスチューブを接合部及び配線用口出し線にかぶせる。測温素子の出口線で配線用口出し線をからげハンダ接合する。*ハンダが全面に良くまわったことを確認すること。
接合部1本づつを0.05×19W テフロンテープで絶縁後、SRワニスガラスチューブを被せる。
スロットライナー入れ
指定の絶縁紙を切断する。スロットに絶縁紙を挿入する。
コイル入れ
揚げコイル(コイルピッチ×2のコイル数)を行いながら、順次コイルを入れる。*スロット底、コイル段間及びコイル側面に、スペーサ挿入の図面指定がある場合は忘れないで入れること。
分割で長さが違う場合は、短い方を結線側に入れること(含浸時、ズレることがある)。また重ならないよう注意のこと。コイルエンドの長さ寸法を確認のこと。コイルが複数ある場合は、コイルクミ図または結線図にてコイル入れ位置を確認すること。測温素子は図面指定スロットのコイル間に入れること。
揚げコイル終了部より、コイル入れ後クサビ打ちを行う。クサビが素手で動かないよう、クサビ下を入れること。コロナ防止積厚板のクサビ下を入れる場合は、t0.9、t0.45、t0.3より選択組合わせ、クサビが素手で動かないよう調整すること。コイルエンドの長さ寸法を確認すること。クサビ打ちは、数スロット分まとめて作業しても良い。
コイルとコイルササエワ間の縛りを行う。結び目には、ほどけないよう接着剤を湿布すること。
前4,5項を繰り返し、揚げコイル(コイルピッチ×2のコイル数)部手前までコイル入れを行う。
写真撮影 コイル入れ工程中(結線側、反結線側) 舟底を使用した場合は、舟底を取り除く。
揚げコイルの下をくぐらせながら、コイル入れを最後まで行う。上口側コイルの吊りヒモを一本づつ切り、コイル入れを行う。
下口側コイル縛りの残った部分の縛りを行う。結び目には、ほどけないよう接着剤を塗布すること。
残ったクサビ打ちを行う。写真撮影 コイル入れ完了(結線側、反結線側)
クサビ固定
上口コイル縛り(図面指示のある場合)
コイルターン間絶縁耐圧試験
マスター波形をメモリーにより表示し、残りの各コイルに印加したサージ波形がマスター波形と同じ波形であることを確認する。→結果をチェックシート「SA-113-7001」に記入する。
マスター波形は型式毎に設定し、標準波形として各試験時に使用する。
絶縁試験
ヨリ線をからげる時は必ず、上口出と下口出を隣接させ1回以上巻き付けること。外れないようにしっかりくわえること。
絶縁抵抗測定 測定前のバッテリーチェック、測定後の放電処理を忘れずに行なうこと。
鉄心押さえ(フレーム)にアース線を取り付ける。口出し部に高圧コードを取り付ける。
絶縁耐力試験(耐電圧試験)
結線方法
シリース接続
上口、下口の口出線長さをそろえ指定寸法に切断する。上口、下口の口出線を接合する。
〈ハンダ接合の場合〉
(1)指定のクリップを接合部に挿入する。(2)必要ある場合は、STコアクミを倒立させ、結線側を上にする。(3)STコアクミを倒立させた場合は、作業台をコア内部に設置する。(4)加熱されたハンダゴテを接合部に当て、加熱後ハンダ(Φ2.3ヤニ入りオール錫)を溶かし込み、接合する。
*ハンダが吸い込まれた全面に良く廻ったことを確認すること。*溶けたハンダでコイルを傷つけないよう ウエス等で保護すること。
〈ろう接合の場合〉
(1)口出し接合面の汚れがないことを確認する。*表面が汚れている場合は、サンドペーパーで磨くこと。(2)接合面がピッタリくっつくよう接合面の変形を修正する。(3)全接合面にりん銅ろう箔を挟む。(4)クランプでコイル口出し線口出し部を咥えた後ろう付機で抵抗ろう付けする。*加熱部の色が暗赤色(約650℃)の状態で通電を止めること。(ピンク色になるまで加熱しないこと)*りん銅ろうが全面に良く廻ったことを確認すること。
〈圧着接続の場合〉
(1)規定の圧着工具により作業を行う。
シリース部絶縁
外部口出し取り付け
指定の口出し線をコイル口出し位置から、外部端子位置迄の長さ寸法に約200㎜余裕をみて切断する。口出し線の片側を口出し線の線サイズの0.5~3.4倍の長さの被覆をむく。
接合部をワイヤジョイントする。*有効締付け寸法は、口出し皮むき長さの1/2以上とすること。ジョイントワイヤの端末処理に突起がないこと。
加熱したハンダゴテを接合部にあて、加熱後ハンダ(Φ2.3ヤニ入りオール錫)を溶かし込み接合する。*ハンダが吸い込まれ、全面に良く廻ったことを確認すること。*溶けたハンダでコイルを傷つけないようワニス等で保護すること。
外部口出し接合部絶縁
ワタリ結線(取り付け)
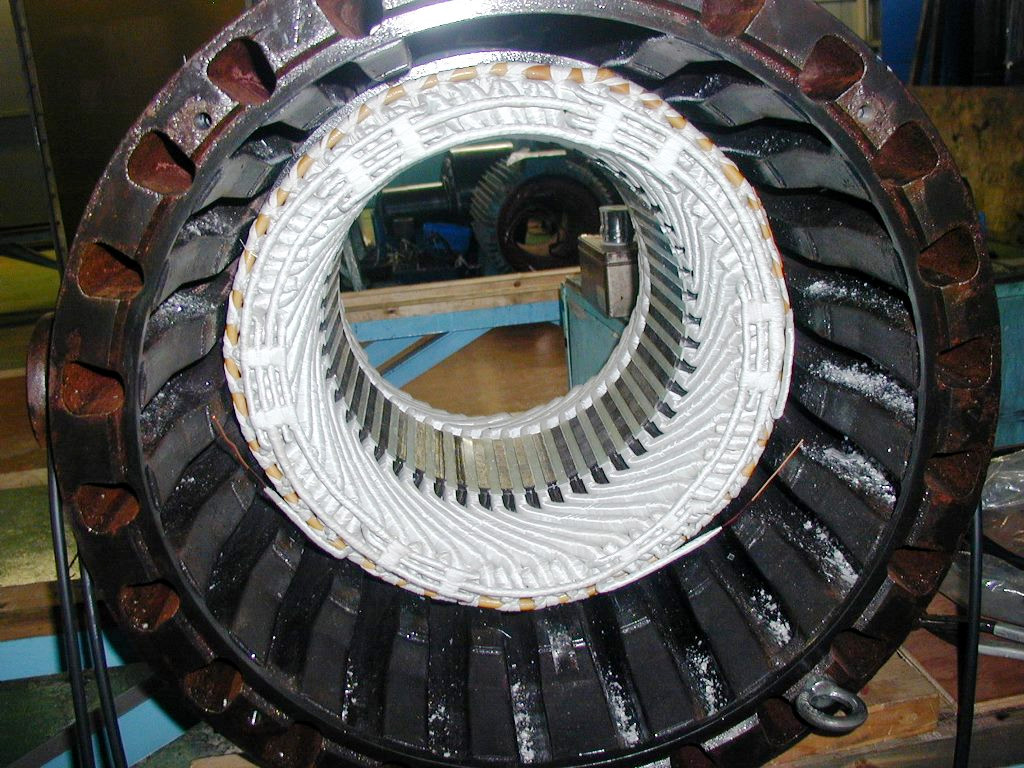
〈ハンダ接合の場合〉
(1)指定のクリップを接合部に挿入する。*クリップおよびコイル口出し線がハンダメッキされていること。(2)加熱されたハンダゴテを接合部に当て、加熱後ハンダ(Φ2.3ヤニ入りオール錫)を溶かし込み、接合する。*ハンダが吸い込まれた全面に良く廻ったことを確認すること。*溶けたハンダでコイルを傷つけないよう ウエス等で保護すること。
〈ろう接合の場合〉
(1)口出し接合面の汚れがないことを確認する。*表面が汚れている場合は、サンドペーパーで磨くこと。(2)接合面がピッタリくっつくよう接合面の変形を修正する。(3)全接合面にりん銅ろう箔を挟む。(4)クランプでコイル口出し線口出し部を咥えた後ろう付機で抵抗ろう付けする。*加熱部の色が暗赤色(約650℃)の状態で通電を止めること。
(ピンク色になるまで加熱しないこと)*りん銅ろうが全面に良く廻ったことを確認すること。
〈圧着接続の場合〉
(1)規定の圧着工具により作業を行う。
結線工程中写真撮影(結線側)結線完了写真撮影(結線側)
ワタリ線絶縁
ワタリ線部固定
測温素子導通試験
コイル間スペーサ挿入
工程内検査(巻線抵抗値測定)
mΩハイテスタをU、V間に接続して抵抗測定する。(巻線抵抗値測定)コイルが3本並列の場合、ヨリ線でからげるか、別のクリップで加えたところにmΩハイテスタのリードを接続するとよい。有効数字が3桁となる様、測定範囲を調整し測定すること。
同様に、V-W間、W-U間の抵抗を測定する。測定値はmΩハイテスタのT・CスイッチONにより20℃換算表示で測定すること。ちなみに、温度が10℃高くなると49%抵抗値が大きくなる。換算機能が無い場合は、次の式で換算する。
補正抵抗値=(235+物温)÷255×測定抵抗値
抵抗値に異常のある場合は、グループリーダに連絡すること。→結果をチェックシート「SA-113-7001」に記入する。1)3φモードにセットし、3φコードを各部出口部に接続する。2)アースコードを鉄心又は、フレームに取り付ける。
(アマライザー試験)
切り替えスイッチを回して各相間(口出し線間)のテストを行なう。波形の第2波以降のズレがあった場合は、グループリーダに連絡のこと。第1波頭の高さが5%以上異なる場合も、グループリーダに連絡のこと。→結果をチェックシート「SA-113-7001」に記入する。”
(極性試験)
結果をチェックシート「SA-113-7001」に記入する。
リード線の三相を接続する。ヨリ線をからげる時は必ず、1回以上巻き付けること。外れないようにしっかりくわえること。
(絶縁抵抗値測定)絶縁抵抗値測定
口出し部に高圧コードを取り付ける。パトライトをセットし鳴らす。絶縁抵抗計を1000Vにセットし、1分間後の抵抗値(MΩ)を測定する。結果をチェックシート「SA-113-7001」に記入する。
(耐電圧試験)耐圧試験
耐圧試験機のツマミをゆっくり回して規定電圧まで速やかに上昇させる。3300V時 7,600V、6600V時14,200V”
規定電圧になってから1分間保持する。→結果をチェックシート「SA-113-7001」に記入する。”
しばり・まとめ各部寸法確認
取付後、コイルエンド外周寸法内に入っているか、ガバリで、チェックする。次の事項を最終再チェックする。コアの結線側・基準スロットが図面通りか。結線方法は図面通りか。各部最大寸法は図面通りか。コア、コイルの傷の無いこと。→結果をチェックシート「SA-113-7001」に記入する。
9、含浸
STコイル予熱
真空引き
STコイルをクレーンで吊りそのままワニスタンクの中に入れる。真空ポンプを起動する。
含浸
2.規定の圧力以下になってから指定時間保持する。
大気圧戻し
加圧
大気圧戻し
ワニス戻し
取り出し
乾燥
写真撮影
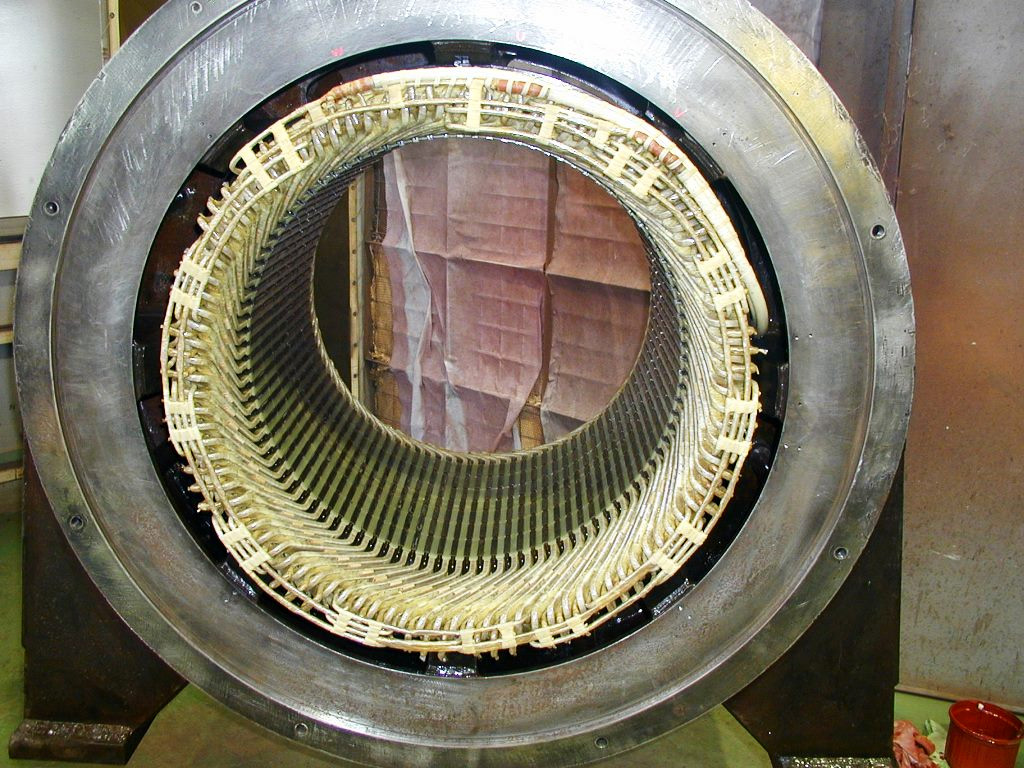
10、仕上げ・検査
樹脂の清掃
養生品の取り外し
リード線取り付け
写真撮影
ワニス塗付け
乾燥
銘板・付属品取り付け
銘板・付属品の取り付け
最終電検(抵抗値測定)(アマライザー試験)(絶縁抵抗値測定)(極性試験)(耐電圧試験)(直流吸収試験)(誘電正接試験)
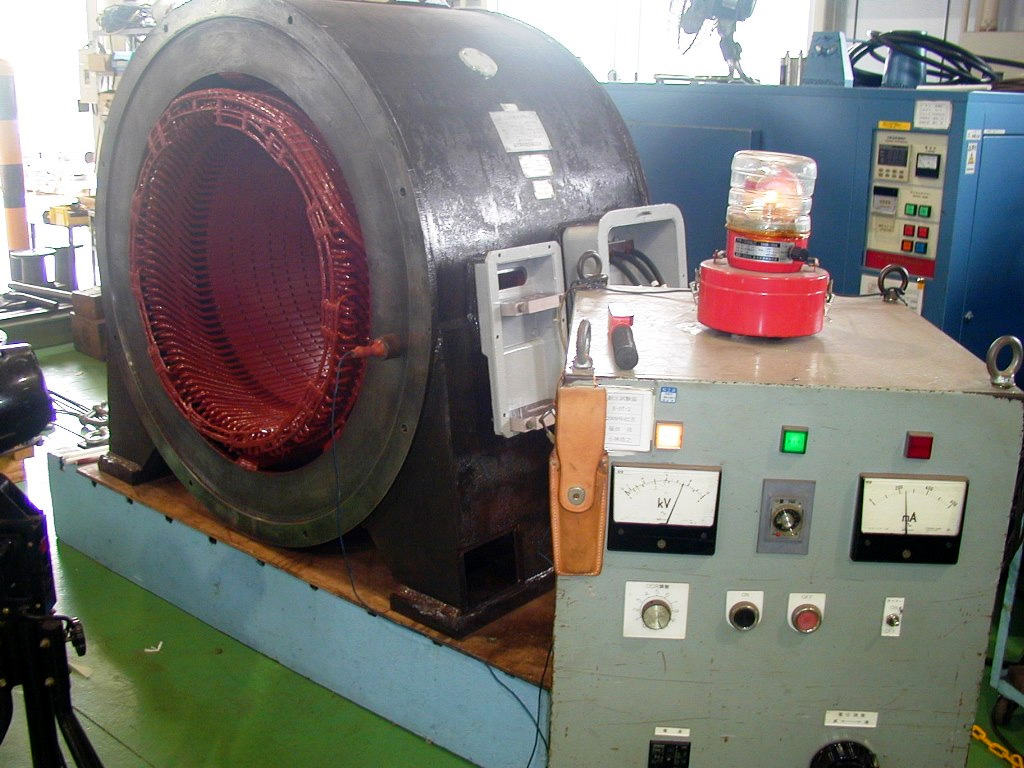
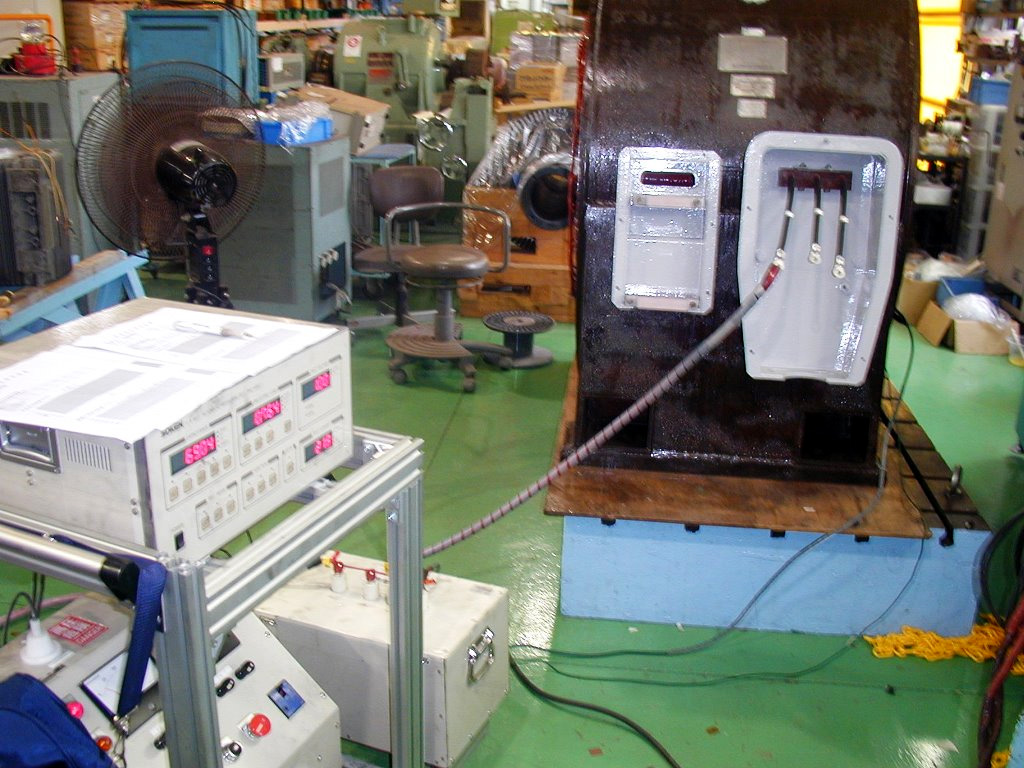
3φモードにセットし、3φコードを各部出口部に接続する。アースコードを鉄心又は、フレームに取り付ける。アマライザー試験 電圧較正カーブにより、口出し線間に5,000V印加となるよう試験機のスライダックを回して、ブラウン管面の振幅を合わせる。
切り替えスイッチを回して各相間(口出し線間)のテストを行なう。
第1波頭の高さが5%以上異なる場合も、グループリーダに連絡のこと。→結果をチェックシート「SA-113-7001」に記入する。
極性試験。サイリスタ整流器のクリップを取り付ける。サイリスタ整流器の電源を入れる。方位磁石により三相、各極が切り替わっていることを確認する。
結果をチェックシート「SA-113-7001」に記入する。リード線の三相を接続する。ヨリ線をからげる時は必ず、1回以上巻き付けること。外れないようにしっかりくわえること。
絶縁抵抗値測定。測定前のバッテリーチェック、測定後の放電処理を忘れずに行なうこと。鉄心押さえ(フレーム)にアース線を取り付ける。
口出し部に高圧コードを取り付ける。
パトライトをセットし鳴らす。絶縁抵抗計を1000Vにセットし、1分間後の抵抗値(MΩ)を測定する。結果をチェックシート「SA-113-7001」に記入する。
耐圧試験。パトライトをセットし鳴らす。耐圧試験機のツマミをゆっくり回して規定電圧まで速やかに上昇させる。3300V時 7,600V、6600V時14,200V”
規定電圧になってから1分間保持する。→結果をチェックシート「SA-113-7001」に記入する。
直流吸収試験(成極指数(PI)試験)、DC1000Vを印加し1分値及び10分値の比較をする。→結果を絶縁診断結果報告書に記入する。誘電正接試験(tanδ試験)、23.3300V時1.0kV、1.5kV、1.7kV、2.0kV、2.2kVを印加、6600V時1.0kV、2.0kV、3.0kV、3.8kV、4.0kV4.8kVを印加→測定結果を絶縁診断結果報告書に記入する。
社外電検依頼時(フル絶縁診断時)
11、塗装
下地処理
塗装材料の配合
噴き付け塗装作業
写真撮影
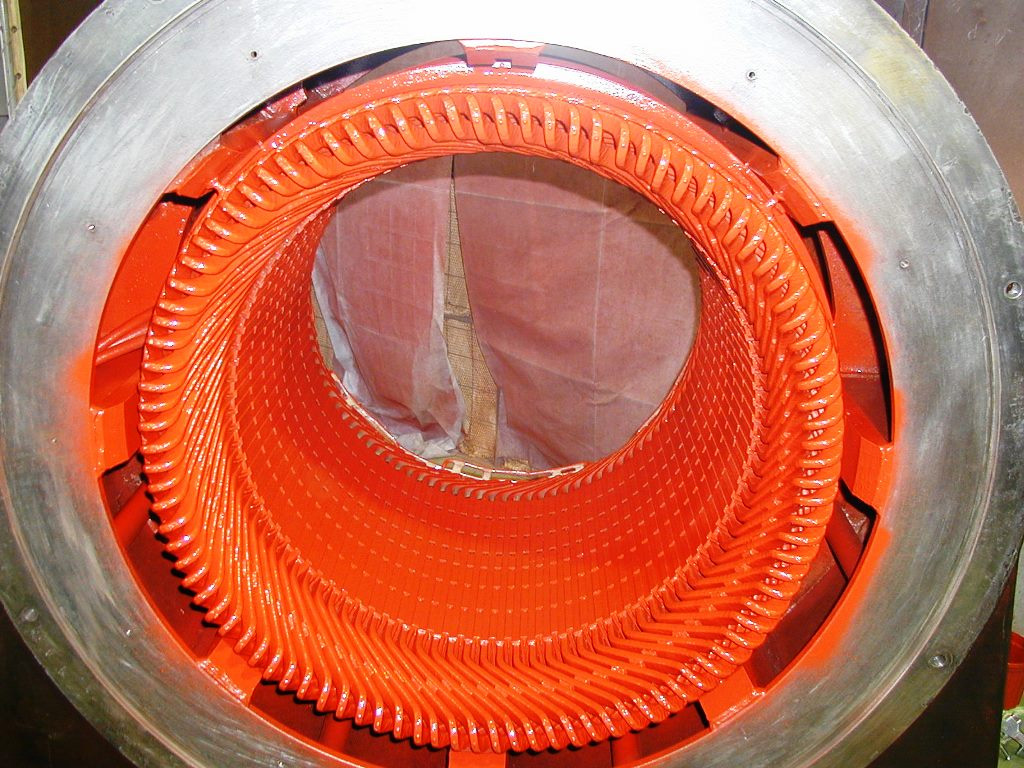